Over the years, I’ve had the pleasure of visiting a variety of equipment and apparatus manufacturers, and recently found myself back at Pierce Manufacturing for a media event. It had been a while since I visited Appleton, Wisconsin, and it was amazing how much things had changed since my last visit.
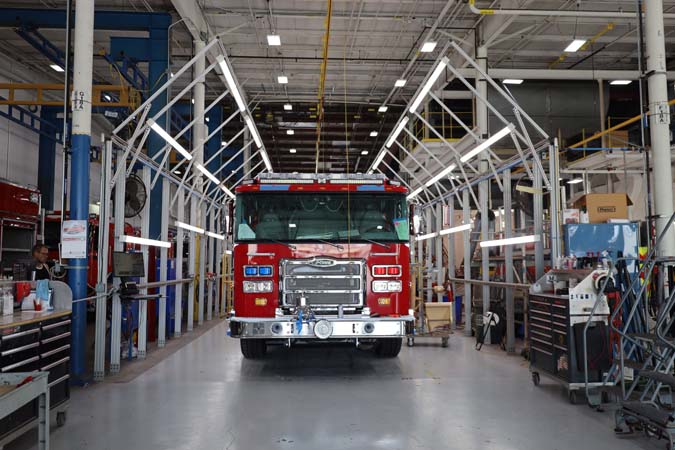
Besides sitting down with other fire service media members, which is always enjoyable, we all had an opportunity to speak with a variety of Pierce representatives starting with Bob Schulz, president of Pierce. Schulz kicked day 1 off with an overview of Pierce’s status right now. For example, the organization is approaching 4,000 team members—and it’s a tenured workforce. Production employees have an average of 12 years with the company and have had two employees achieving 50 years with the company.
As many know, Oshkosh Corporation owns Pierce, and Schulz stressed how important that is to Pierce’s financial stability as well as how it allows continuous innovation. TAK-4 suspension, E-Coat—these are just two examples of many Oshkosh technologies integrated into Pierce rigs. Schulz also highlighted the strength of Pierce’s dealer network, a network which was brought throughout the day.
Schulz also stressed that the company will not sacrifice the safety of its employees or the quality of its products to benefit delivery (see video above.).
Our first stop on the tour was to the IPP Plant. This is the fabrication plant. Bill Kurtzweil, an 18-year veteran of Pierce who said he “bleeds 90 red” led the tour. This leg of the tour very clearly represented how Schulz described Pierce employees: craftspeople. Pierce builds its rigs from the ground up, and media members were able to witness cabs and bodies being fabricated from the start. One point Schulz made in the morning was how being owned by Oshkosh allows Pierce to invest in its operations, and Kurtzweil explained at many stops on the tour how investments Pierce has made in tools over time has allowed Pierce to increase efficiencies when it comes to fabricating parts for the cabs and bodies. IPP was originally constructed in the 1970s and has been added onto twice over the years, yielding a facility that is approximately 280,000 square feet—another example of reinvestment.
One feature of the plant was an area set aside for 10 apprentices year-round to serve as a pipeline for the next generation of workers. Here, high schoolers will apprentice as welders and be evaluated for future employment as fabricators. Kurtzweil added that the apprentices can track up from there within the company.
From IPP, media members made their way to “CBN.” This is the company’s Neenah facility, and it’s where Oshkosh Striker aircraft rescue and firefighting (ARFF) vehicles are manufactured as well as where cabs are assembled. CBN also is where the company’s chassis line is located. Media members saw step by step how cabs and chassis are assembled.
After lunch, we all toured the ASY plant—the Assembly plant. Dan Meyer, vice president of sales at Pierce, was our guide for this portion. The rigs end up here when the bodies are mounted to the cabs/chassis as they approach the “Blue Floor” where final inspection takes place. This facility also houses massive pain booths, the graphics department, corporate offices, the “light tunnel,” as well as a paint shop that contains paint chips for Pierce’s 369 red colors (including Pierce’s most popular: 90 Red), 129 white colors, and other specialty colors. I probably heard, “Chris, when you were here last time, this section was for x,” the most in this facility. Pierce completed an additional 90,000 square feet addition to this facility in 2022, which meant many stations in the process have been moved around. Of interest to customers is that Pierce is also expanding the Blue Floor, allowing more final inspections to take place at the facility.
Pierce works to establish a baseline for its production employees, and has a training center where new employees go through a “basic training” to develop their skills. The program can be up to four to six weeks, and is designed for success. Instructors will give new employees what they need to succeed if they identify an area in which an employee is struggling. The training center also has an aftermarket training area, which is in line with Pierce’s pledge for service through the lifetime of the vehicle and rolls into our next stop: the Global Logistics Center (GLC).
The GLC is almost a company within a company. Its customers are Pierce Dealers and operate out of a 90,000 square-foot warehouse. If it does not have a part it can generally be fabricated and shipped quickly. It ships approximately 400 packages/day. The GLC ensures that parts for your Pierce vehicle will be available for its lifetime.
It was a packed day, but one that revealed how Pierce has reinvested in its operations over the last several years, which has helped it increase its capacity to meet very high demand for new rigs in recent years. There will be more to come at a technical school later this week, and the media event will culminate with Pierce’s 9/11 Memorial Stair Climb.