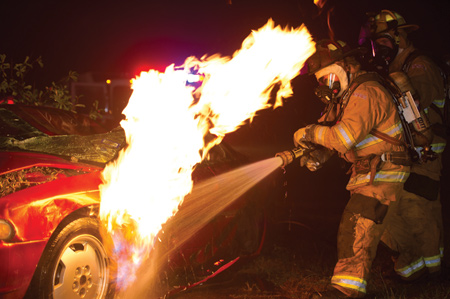
Structural firefighting personal protective equipment (PPE) has three layers of protection: an outer shell, a moisture barrier, and a thermal liner. Each of those layers uses a different type of fabric to provide the firefighter with a safe envelope in which to work.
Fibers
Bryan Bolden, senior sales and marketing manager for PBI Performance Products, says his company makes fibers that go into the fabrics that are crafted into the various turnout gear layers. “The principle behind the PBI fiber is that it is more flexible, allowing a firefighter to do the job more efficiently and putting less stress on firefighters because of their turnout gear,” Bolden says. PBI’s latest innovation is the PBI Lightweight Gold system, says Brian Shiels, PBI’s senior development engineer. The system uses either PBI Matrix or PBI Max fabrics made by Safety Components or Kombat Flex made by TenCate Protective Fabrics as the outer shell, a Stedair Gold moisture barrier, and a thermal liner of Glide with PBI G2 or TenCate’s Quantum4. “The system is about a pound lighter for all the fabrics, but it’s more flexible, so there is more perceived comfort for the wearer,” he says. “It’s also easier to don and doff the gear.”
DuPont Protection Technologies makes two fibers often found in turnout outer shells-Nomex® and Kevlar®. Nomex fiber offers inherent flame resistance while contributing toughness and flexibility to outer shell fabrics, says Dennis Mater, DuPont Nomex sales technical leader for apparel in North America. “Nomex fiber thickens and carbonizes when exposed to intense heat from flames,” he says. “This action increases the protective barrier between the wearer and the heat source, helping to reduce burn injury and providing valuable time to work or escape.”
1 Globe Manufacturing makes use of twill weave and both spun and filament yarns in the fabrics it uses for structural firefighting turnout gear. (Photo courtesy of Globe Manufacturing Inc.) |
DuPont Kevlar is one of the toughest fibers available on the market, Mater maintains. “On an equal weight basis, Kevlar fiber is five times stronger than steel,” Mater says. “Yet fabrics made with Kevlar fiber can be lightweight, comfortable, inherently flame-resistant, and thermally protective. Kevlar fiber contributes to the overall durability and strength of lightweight turnout gear outer shell fabrics, enhancing strength and protecting the moisture and thermal barriers inside.”
Mater points out that while Nomex and Kevlar fibers are used extensively in the layers of firefighter turnout gear, 70 percent of turnout gear’s thermal protection comes from the inner components made of Nomex and Kevlar fiber.
Fabrics
Safety Components makes PBI Max, its newest PBI outer shell fabric, according to Guy Lucas, director of marketing, where the technological design gives firefighters the best combination of break-open and thermal protection, the strongest outer shell fabric, comfort, and flexibility. The weight of PBI Max is seven ounces per square yard (osy).
Another Safety Components outer shell fabric made from PBI fiber is PBI Matrix that combines the heat and flame protection with a durable matrix of high-strength 400- or 600-dernier filaments to reduce wear and tear. This results in high-performance flame and break-open protection, increased abrasion resistance, and improved tear resistance, Lucas says.
Safety Components also makes Armor AP, Armor 7.0, and Fusion outer shells for structural firefighting turnout gear. Armor AP uses filament twill technology to improve mobility and durability of its 40 percent DuPont Nomex and 60 percent DuPont Kevlar fabric. Armor 70 also uses filament fiber technology, combined with military-grade, ballistic-filament DuPont Kevlar and Nomex fibers. Fusion fabric blends Kevlar, Nomex, and Teflon® F-PPE for thermal protection, longevity, abrasion resistance, and water repellency.
2 Lion’s V-Force structural firefighting gear is manufactured with a user’s choice of fibers and fabrics for its outer shell, from PBI Max, Kevlar, Armor AP, Nomex, and others, along with an assortment of moisture and thermal barriers. (Photo courtesy of Lion.) |
TenCate Protective Fabrics makes several outer shells for structural firefighting. It’s newest fabric, TenCate Kombat Flex, is made with a blend of PBI and DuPont Kevlar fibers reinforced with Kevlar filament, according to Michael Cheek, TenCate’s marketing manager. He notes that TenCate’s textile engineers developed a proprietary manufacturing method to make Kombat Flex a perfect balance of strength and softness.
TenCate’s Millenia XT outer shell fabric provides the strongest, most durable outer shell for departments with the most demanding calls, Cheek notes. Millenia XT is a para-aramid/PBO fabric with high thermal stability that retains its strength even after exposure to heat, is durable, and has a supple hand that enables greater freedom of movement. The “hand” of a fabric refers to the feel of the fabric against the skin.
Many jurisdictions with a wide range of responses but with a need for the most bang for the buck, he adds, choose TenCate Ultra fabric for their outer shell. Earlier this year at FDIC International 2015, TenCate’s product development team exhibited turnout gear made with a concept fabric that, as yet, is unnamed, Cheek says. The textile highlights TenCate Enforce technology, which allows it to make fabrics lighter and more flexible that maintain the strength of outer shells 10 percent or more heavier. Cheek says TenCate expects the new outer shell to join its S-Series later this year.
Jennifer Wise, structural firefighting marketing specialist for W.L. Gore, says that while Gore doesn’t make turnout gear outer shells, it does make moisture and thermal barriers-two critical components in turnout gear design and protection for the firefighter. “Breathability and resistance to sweat impact are the most important things firefighters are concerned with in their moisture barrier,” Wise says. “Our technical team wanted to make a big shift in breathability, so we developed the Gore Parallon Liner System, which is a moisture barrier and thermal protection barrier together in a single system.”
In the Gore Parallon Liner System, the moisture barrier sits closer to the skin, which Wise says helps drive higher breathability. “In a typical thermal liner, a firefighter could lose a third of his thermal protection because of sweat, but Parallon takes care of that issue and adds consistency to thermal protection.” Gore also makes Crosstech 3, a three-layer moisture barrier; Crosstech Black, a two-layer moisture barrier; and the Gore RT7100 moisture barrier.
Stedfast, Inc. makes three moisture barriers used in structural turnout gear. Stedair 3000 has a Teflon moisture barrier laminated with DuPont Nomex E-89 substrate to help firefighters stay cooler and more comfortable while providing protection against water penetration. Stedair 4000 is a tricomponent moisture barrier, combining a woven 3.2-opy DuPont Nomex pajama check substrate with an enhanced bicomponent membrane composed of expanded PTFE (Teflon) matrix and oleophobic (oil-hating) polymer coatings impregnated into the fabric. Stedair Gold combines a high-performance PBI fiber with DuPont flame-resistant fibers for high fire resistance and maximum breathability.
Structural Turnout Gear
Mark Dolim, national sales manager for Globe Manufacturing Inc., says that Globe is “agnostic when it comes to suppliers of fabrics and fibers. We buy from all of the mills.” Dolim notes the new twill weave fabrics are gaining in popularity among firefighters. “The fabric drapes very nicely on the body, and it is softer and more flexible than previous fabrics,” he says. “It imparts an immediate sensation of comfort and improved range of motion.”
Dolim says both TenCate’s Kombat Flex and Safety Components’s PBI Max use a twill weave and both spun and filament yarns. “Filament yarn is like fishing line,” he says. “It’s extruded and has incredible tensile strength. Spun yarns blend Nomex and Kevlar or Kevlar and PBI that are shorter fibers spun into yarn. They typically have better abrasion resistance and provide more comfort for firefighters.”
Dolim notes that Globe has turnout gear that offers high tear strength, high insulating qualities, abrasion resistance, and flame protection. “We have 18 outer shells that embody the different characteristics of the fibers from which they are made,” he says. “We also offer a half dozen moisture barriers and a dozen thermal barriers. The choice of the various layers is up to the risk assessment that each fire department makes.”
Michael Laton, senior product manager for body protection at Honeywell First Responder Products, says Honeywell has five Morning Pride lines, many sold with fabric made with PBI continuous reinforced filaments. “Continuous filament yarn has a much higher strength compared to spun yarn,” Laton points out. “At the same time, it can reduce the weight of the fabric while increasing its strength. What used to be 7.5-opy fabric now is 7.0-opy or 6.9-opy but with an increase in the fabric’s tear and breaking strength.”
While most top-of-the-line turnouts have outer shells made with continuous filament yarns, the midrange outer shells continue to be dominated by a 60/40 percent blend of Kevlar and Nomex fibers, Laton says. “Typically they are spun fabrics, but the mills are looking at rolling continuous filament yarns into the midrange product line, which would give a higher strength, more flexibility, and good hand at a lower price point.”
Steve Allison, director of sales for Fire-Dex, believes that firefighters have always been concerned about the longevity of their turnout gear. “Durability is very important, and strength and comfort are important concerns too,” Allison says. “As manufacturers, we focus efforts on making our gear comfortable, yet strong.” Fire-Dex makes the FX-R turnout gear that is customizable from any of the turnout gear outer fabrics. The FX-R gear has a seamless collar, shoulder seams moved inward to the natural bend point, prebent knees and elbows, and an athletic-cut pant with a seamless gusset. Allison thinks the turnout gear market will continue to see advances in weave design. “We will see continued improvement there,” he says, “maybe some lighter weights, and patterning or shading that will change the look of the gear.”
Karen Lehtonen, vice president of innovation and product management for Lion, says Lion approaches the manufacture of turnout gear differently. “We don’t approach it as three layers being separate entities,” Lehtonen says. “We look at them as a system and how they perform together, with mobility and flexibility working to provide safety and comfort for the firefighter.”
With outer shells, Lion looks for fabrics that are lighter weight yet still provide high strength and have good thermal characteristics, Lehtonen points out. “We use a lot of PBI Max with filament twill technology, filament Kevlar, and PBI spun yarn in a twill weave, as well as Armor AP, a Nomex and Kevlar blend in a twill weave from Safety Components.”
Lehtonen says that when Lion pairs flexible fabrics with its ergonomically designed V-Force turnout gear, the fabrics enhance the mobility features designed into the gear and make the firefighter more efficient working in the turnouts. Lion also uses the Isodri moisture management system in its turnout gear, a thermal liner that both wicks and sheds water. A face cloth wicks perspiration away from the undergarment and channels it to a layer or layers of DuPont Nomex E-89 treated with Teflon F, which sheds the moisture.
ALAN M. PETRILLO is a Tucson, Arizona-based journalist and is a member of the Fire Apparatus & Emergency Equipment editorial advisory board. He served 22 years with the Verdoy (NY) Fire Department, including in the position of chief.